![[Alt]](/upload/iblock/3fb/o1cwy2qpuxgnvdt4m1mv2vk2nl2sjv5c.png)
Robotic Cutting Solutions
Automate the cutting process at your facility and gain an edge over your competitors.Robotic cutting is the automation of material cutting using industrial robots. This method significantly enhances cutting precision, speed, and efficiency, reducing costs and increasing productivity.
-
30%increase in
productivity -
20%reduction in
production
costs -
24/7cutting
robot operation -
1+ years
average return
on investment
![[Alt]](/upload/iblock/b00/he8fbtfcx70po59k1loqvci0an3shnvb.png)
Industries
Material cutting robots are used in various industries where precise, efficient, and automated cutting processes are required. Here are some key application areas:
Consumer Goods Manufacturing
Robots are employed to cut a range of materials such as plastic, glass, and metal, enabling the production of high-quality goods with minimal costs.Construction
In the construction industry, robotic cutting is used for the precise processing of building materials like steel and concrete, improving construction quality and speeding up project completion.Automotive Industry
In the automotive sector, robots perform precise cutting of metal and plastic parts, ensuring high product quality and reducing assembly time.Aerospace Industry
Robotic cutting allows for the creation of complex and precise components for the aerospace industry, meeting high standards of quality and reliability.
Types of Robotic Cutting
There are several types of robotic cutting, each utilizing different methods and technologies to cut various materials. The main types include:
Laser Cutting
Uses a laser beam for precise cutting of various materials. It offers high speed and accuracy, suitable for cutting metals, plastics, and composite materials.Plasma Cutting
Uses a jet of plasma to cut metals. It provides high speed and efficiency, suitable for cutting thick and hard materials.Waterjet Cutting
Uses a high-pressure stream of water mixed with abrasive materials for cutting. Suitable for a wide range of materials, including metal, stone, and glass.Mechanical Cutting
Involves using various mechanical tools such as saws and milling machines for cutting materials. It is applicable to a wide range of materials and is used in various industries.
Components of a Robotic Cutting System
A robotic cutting system typically includes several key components that work together to automate the cutting process. The main components are:
1. Robotic Manipulator
The main element that moves the cutting tool along the specified trajectory. It can have various degrees of freedom (from 4 to 6 or more).2. Cutting Tool
Depending on the material and task, this can be a laser cutter, plasma cutter, waterjet cutter, milling tool, or another cutting device.3. Control System
A computer with software for creating and editing control programs, as well as managing all aspects of the system's operation, including robot movement and cutting parameters.4. Robot Controller
A device that converts commands from the control system into robot movements and cutting tool operations.5. Material Handling System
Mechanisms for automatically feeding workpieces into the cutting area and removing processed parts. This may include conveyors, manipulators, CNC tables, and other devices.6. Workpiece Holding System
Devices for securely holding the material being processed during cutting. Various clamps, vacuum tables, etc., may be used.7. Sensor and Monitoring System
Includes position, speed, force sensors, and others, as well as cameras for visual process control. The monitoring system allows for tracking the condition of the system and the quality of the cutting.8. Safety System
Includes guards, light barriers, emergency stop switches, and other elements ensuring the safety of personnel.9. Operator Interface
A control panel or computer interface for operator interaction with the system, including tools for program input and adjustment, process monitoring, and diagnostics.10. Cooling and Waste Removal System
For laser and plasma cutters, this can include cooling systems for the cutting tool and systems for smoke and dust removal.
Robots for cutting application
Benefits of Implementing a Robotic Cutting System
Robotic cutting can address several challenges that traditional cutting methods cannot achieve at the same high level. Let's consider each of these benefits in more detail:
High-Precision Cutting of Complex Parts
The high repeatability of movement allows the robot to cut with perfect precision along even the most complex paths.Reduced Material Processing Time
Robots work at high speeds, delivering quick and precise cuts without the need for breaks and rest.Reduced Labor and Material Costs
A robotic system replaces human labor, thus freeing up the workforce and minimizing material waste, which is especially important when working with expensive or scarce materials.Increased Production Safety
The use of robots for cutting enhances worker safety and reduces the risk of occupational injuries and accidents.
Contacts
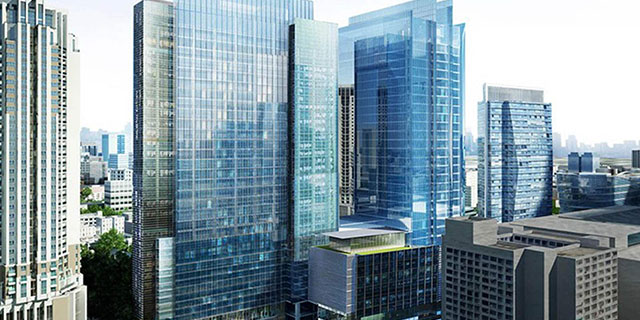
35th floor, 33/4, Tower A Rama 9 Road, Huaykwang Sub-district, Huaykwang district, Bangkok, 10310
Mon – Fri:
9 AM–8 PM